Thursday 12th January 2023
Question: If you went shopping today for white goods would you buy a cooker with a trade name that you have never heard of, that has no CE or kite testing labelling, very short or no warranty and no technical support?
Hardly a day goes by that I don’t wake up to at least one email or post on social media advertising a cheap laser machine that will create a wonderful range of products from the comfort of your own home! As laser engravers/cutters become smaller and more affordable so the growth in ownership has escalated. This technology that was once reserved for only the most established businesses and heavy industry is now commonplace in the small business sector and particularly among cottage industries with many sole traders operating from home and selling their goods via the internet.
With this in mind it is important that operators are aware of the potential risks and hazards posed by the technology and fully understand the components of their laser cutter and how these combine to form an efficient and safe system.
Safety tips
In addition ensure that your laser cutter has passed independent safety testing by a recognised body like a CE mark. This means that it has been tested to meet European safety and environmental standards and considered safe to use.
Tips
What is fume?
As the laser thermally decomposes the substrate it gives off fume which is a mixture of particulate and gaseous matter. Fume from materials such as metals and glass is mainly particulate, the majority of which is less than 1µ (micron) in diameter. Organic materials, particularly plastics, produce much more complex fumes which require a greater level of extraction. Most of the particles are spherical and roughly 90% by weight are less than 1µ in diameter. These particles fall within the respirable range and need to be removed from the working environment to prevent bronchial or lung damage. These gaseous organic compounds produced are known as Volatile Organic Compounds, VOC's.
The most efficient way to remove fume is by connecting a fully filtered extraction system to the laser. This system intakes the dust and fume from the laser cabinet, feeds it through a series of filters and then expels clean, recycled air back into the environment. The filters are replaced periodically as they fill up. Your laser will have a manufacturer's recommended air flow rating expressed as CFM (cubic feet per minute) or L/m3s (litres per second) ; this will vary according to the size of the work area on your laser.
At this point it is worth mentioning the importance of machine vents and good air circulation. Your laser will have cooling vents normally where fans and controller boards are located. These should not be covered and your manufacturer may recommend a minimal all round clearance to maintain good airflow.
Tip.png)
Safe Lasering!
Hardly a day goes by that I don’t wake up to at least one email or post on social media advertising a cheap laser machine that will create a wonderful range of products from the comfort of your own home! As laser engravers/cutters become smaller and more affordable so the growth in ownership has escalated. This technology that was once reserved for only the most established businesses and heavy industry is now commonplace in the small business sector and particularly among cottage industries with many sole traders operating from home and selling their goods via the internet.
With this in mind it is important that operators are aware of the potential risks and hazards posed by the technology and fully understand the components of their laser cutter and how these combine to form an efficient and safe system.

Fire Warning
A laser beam is a ‘light wave’ of photons that generate energy. These photons, i.e. the ‘light particles’, transfer their energy to the atomic or molecular structure of the material, which in turn causes the material to heat up and generate significant temperatures. Some materials are extremely flammable and can easily burst into open flame setting the machine ablaze. This open flame is very dangerous and has the potential to destroy not only the machine, but the building in which it is housed. Experience shows that vector cutting with the laser has the most potential to create an open flame. Many materials are susceptible to ignition but acrylic, in all its different forms, has been shown to be especially flammable when vector cutting with the laser.
Safety tips
- Do not leave the laser unattended during operation
- Keep a halogen fire extinguisher close to the laser
Laser Class
Lasers are classified for safety purposes based on their potential for causing injury to humans eyes and skin. Most laser products are required by law to have a label stating its Class. It will be listed either in Alpha numerals (1 2, 3R, 3B, 4) or in Roman numerals (I, II, IIIa, IIIb, IV). The lower the class the safer the device will be. A Class 2 or ll laser is typically an encased system which has interlocked doors preventing the laser firing until these are in the closed position. This class of laser is considered safe if used correctly and without the need for additional PPE (Personal Protection Equipment) like goggles.
In addition ensure that your laser cutter has passed independent safety testing by a recognised body like a CE mark. This means that it has been tested to meet European safety and environmental standards and considered safe to use.
Tips
- Ensure your laser cutter is clearly labelled with class and CE marked so you know what PPE (if any) is required.
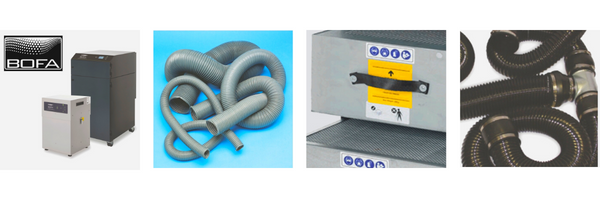
Fume Extraction
Virtually all laser operations whether engraving , marking or cutting will give off different levels of smoke and fume depending on material being converted. It is vital that these elements are removed in an efficient and safe manner to avoid poor quality cutting, potential corrosion of machine parts and danger to the operator.
What is fume?
As the laser thermally decomposes the substrate it gives off fume which is a mixture of particulate and gaseous matter. Fume from materials such as metals and glass is mainly particulate, the majority of which is less than 1µ (micron) in diameter. Organic materials, particularly plastics, produce much more complex fumes which require a greater level of extraction. Most of the particles are spherical and roughly 90% by weight are less than 1µ in diameter. These particles fall within the respirable range and need to be removed from the working environment to prevent bronchial or lung damage. These gaseous organic compounds produced are known as Volatile Organic Compounds, VOC's.
The most efficient way to remove fume is by connecting a fully filtered extraction system to the laser. This system intakes the dust and fume from the laser cabinet, feeds it through a series of filters and then expels clean, recycled air back into the environment. The filters are replaced periodically as they fill up. Your laser will have a manufacturer's recommended air flow rating expressed as CFM (cubic feet per minute) or L/m3s (litres per second) ; this will vary according to the size of the work area on your laser.
At this point it is worth mentioning the importance of machine vents and good air circulation. Your laser will have cooling vents normally where fans and controller boards are located. These should not be covered and your manufacturer may recommend a minimal all round clearance to maintain good airflow.
Air Assist
Most laser machines will have an air assist connected to or close to the lens which is essentially a small compressor blowing a constant jet of low pressure air onto the lasers point of contact, keeping the area cool, avoiding flare ups and reducing scorches.
Tips
- Ensure your laser has adequate extraction making it safe to use and improving the quality of your cut.
- Do not attempt to laser PVC as it gives off harmful chloride gases that are toxic.
Tube Cooling
It is imperative that your laser system has cooling apparatus to prevent the tube overheating and becoming inoperable. There are two main methods a) air cooling b) water chiller. Air cooled systems are normally associated with metal tubes and use a series of fans for the purpose, whereas chillers circulate cold water and are used mostly with glass tubes . It is important that these cooling systems are maintained like cleaning the fans periodically or flushing the water every year and changing the chiller filter every six months
Maintenance
Like any piece of machinery your laser has both static and moving parts. These require regular maintenance to keep them working efficiently and extend their working life. Good housekeeping is essential to safe running and includes cleaning mirrors and lens, emptying vector grids and trays, checking that hose inlets/outlets are clear and replacing filters.
Tip
- Adopt a proactive approach to laser maintenance and have it serviced 1-2 times per year by a trained engineer. Don’t wait for your laser to break down before you carry out maintenance!
.png)
Materials
I have left this subject until last but it could easily be at the top of this article. Cutting and engraving is the primary reason for acquiring the laser in the first place and most users are under the impression that you can buy a laser, pick up some ply from your local hardware store and away you go! Not all materials are laser friendly and products like plywood, MDF and rubber have modified laser specific versions. Know what you are lasering and get the chemical makeup of the material or ask for a material safety data sheet (MSDS) and cross reference it against a material compatible list or our team is on hand to help you with any questions you might have.
Safe Lasering!